
Sintering Oven
Tridelta is among the few companies focusing on the heat treatment of ceramic materials, cofired and single material sintering and debindering. Solutions have been manufactured using different technologies and production volume depending on the customer requirements such as
- Furnaces with protective gas atmosphere for investigation of metal melts
- Furnaces for joining of glass and ceramic parts
- Equipment for the synthesis of powders consisting of nano particles
- Gradient furnaces for pattern testing
- Investigation of materials under pressure, at high temperatures, and in defined gas atmospheres.
General Specification
Usable area100 x 100 mm up to 4.000 x 40.000mm
Temperatureup to 2400 C downto +/-2 K
Typecontinuous, batch,multiple stack
Multiple gasesN2, H2, O2, Ar, …
Machines
R&D/ Lab Kilns

RTP oven TM 100
- Up to 250 K/sec heating up
- Up to 40 K/sec cooling down
- Temperature uniformity up to +/- 0.01% at 1000 C
- Standard up to 8 inch substrate size
- Option up to 1.000 x 1.000mm
- Up to 3 gases
- Hydrogen operation
- Optional Vacuum operation
- Water cooling
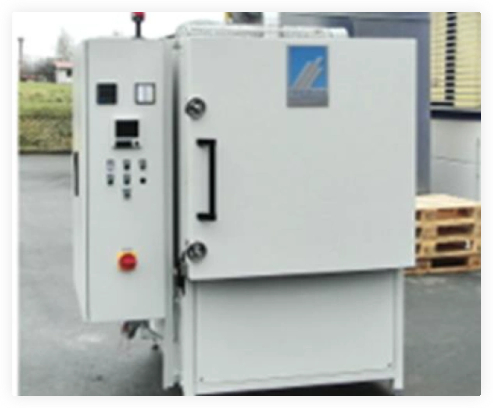
Front Loading batch oven
- Up to +/-3 K Usable Area Uniformity
- Experienced combination of
- Controllers
- Heaters
- Gas flow and inlet ß Insulation
- Rotating air supply through 3 gas entries on each heating side specially designed for De-bindering of materials
- OPTIONAL CO2 measurement device for De-bindering optimization
- Highest quality heating elements
Tower Kilns
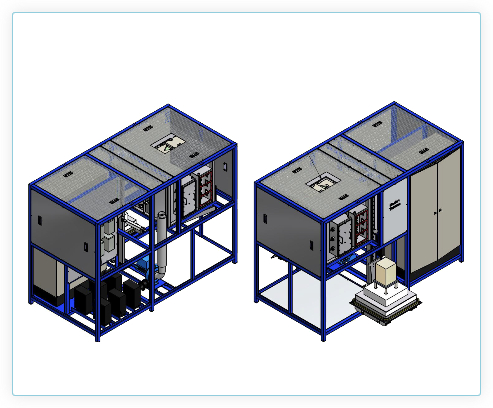
1-Tower
- Temperature up to 2200 °C
- Fired Material example – Al2O3
Inner Dimensions
- Width : 250mm
- Length : 250mm
- Length : 250mm
- Volumne : 15L
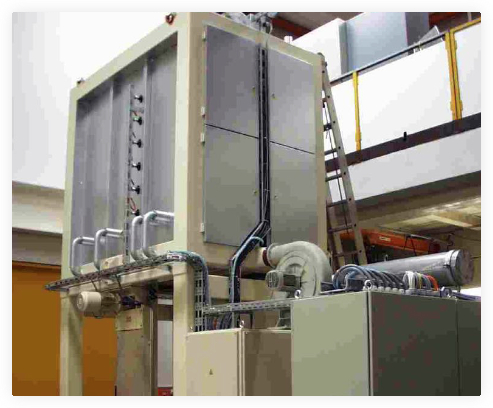
2-Tower
- Up to 2200 °C
- Up to +/-1K uniformity
- Up to +30K ramps
The total installed heating power is dimensioned to the customer’s required temperature (maximum temperature 1,200oC, example operation temperature 950oC) of the kiln chamber. The hearth is pivot-mounted at the lower closing plate of the kiln and is driven by an electric motor outside the kiln.The elevating hearth can be moved into and out of the kiln by a lifting platform with spindle to enable easy loading and unloading of substrates.
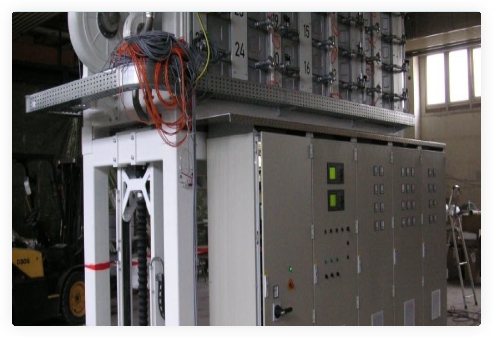
6-Tower
- Up to 2200 °C
- Up to +/-1K uniformity
- Up to +30K ramps
The electrically heated elevating hearth furnace with 6 product stacks serves for debinding and sintering of LTCC ceramics with thermal after-burning and dosage of gas preheated by SiC heat-ing rods. 28 heating groups are implemented.The installed heating power of the SiC rods is 300 kW (at 1000°C and a surface exposure of 10 W/cm2). The installed transformer power is 28 x 11.0 kW (=308 kW).
Rotating Kilns
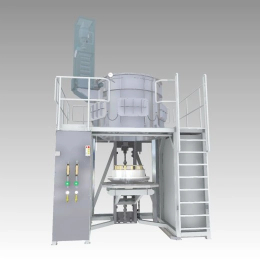
Small kilns
- Inner Diameter ~ 200 mm
- Height ~ 300 mm
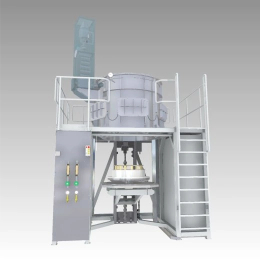
Medium
- Inner Diameter ~ 200 mm
- Height ~ 400 mm
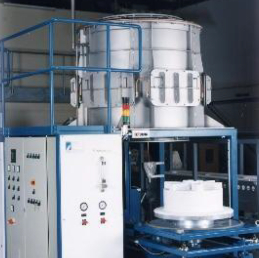
Large
- Inner Diameter ~ 250 mm
- Height ~ 450 mm
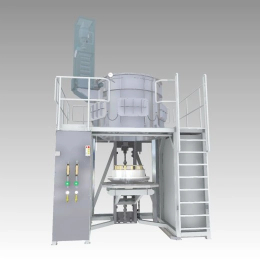
Small kilns
- Diameter ~ 340 mm
- Height ~ 530 mm
Continuous Ovens
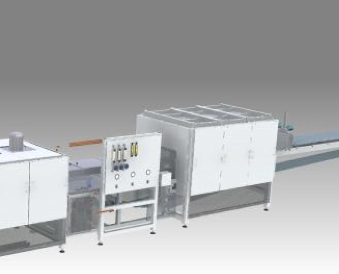
Belt Ovens
- Up to 1200 C
- Width up to 600mm
- H2/O2/… environment
- Full MES control
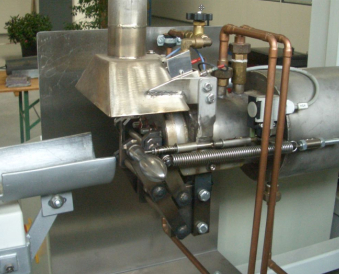
pusher
- Up to 2000 C
- Width up to 600mm
- H2/O2/… environment
- Heat recycling systems
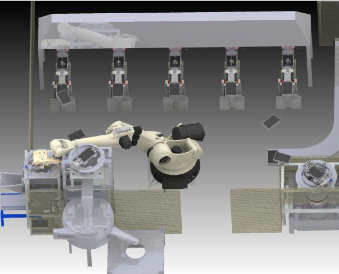
special
- Up to 2000 C
- Robotic loading
- Multistory ovens
- Integrated return
