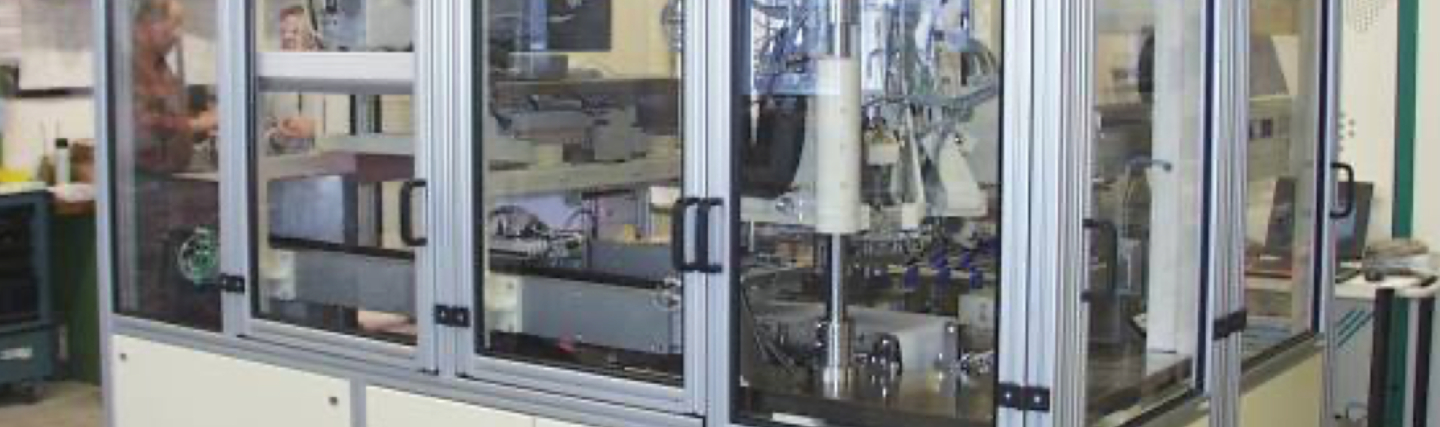
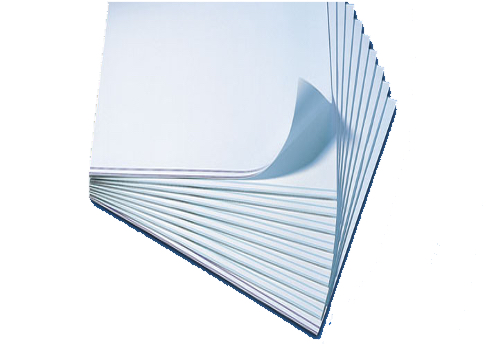
Multilayer Cofired Materials
Using conductive and dielectic layers allows customers to design and product complex circuits with a small footprint. However mostly these materials must also be processed together and therefore need to be able to process under the same conditions most importantly the forming temperatures
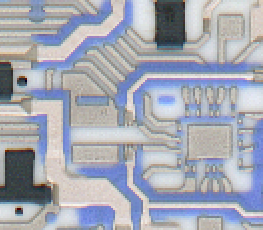
Multi-layer print
Multilayer prints allow the customer to design circuits with crossovers and surface connections with additional building blocks like SMT components to be added to the surface.
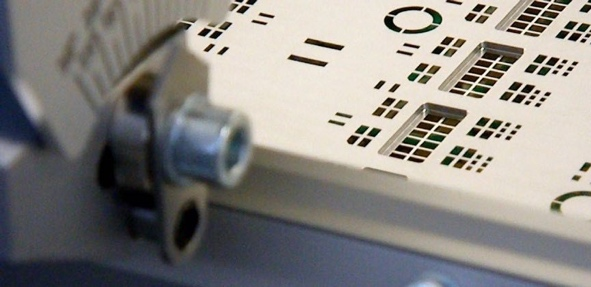
Stencil Print
Stencil print is one of the most economic solutions when producing conductive or dielectric structures. Advantages are in the uniformity of the print and the potential cavities this technology can print in. However other technologies can produce thicker or thinner active and passive layers.
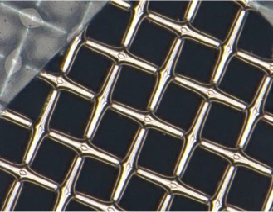
Screen Print
Screen printing is a technology used for creating intricate patterns in a very efficient way. Due to this flexibility and efficiency, the boundries of this technology are constantly being broken down with ever thinner lines and spaces.

Additive / 3D production
Building things from the ground up is in the human nature. However with limited tools we were forced to create some things with destructive methods and create significant waste. Modern design and production tools target to minimize waste and increase efficiency and final products.
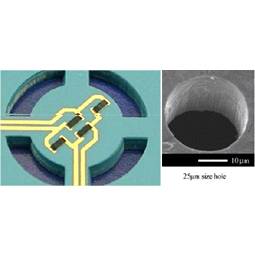
Punching Mechanical Laser
When destructive shaping of products is necessary punching and stampingis often the most precise and economic tool.
In many cases still to today the mechanical punching is the most flexible and fast solution.

Copper Bonding
Melting two products together can result in the best of two worlds. In the case of copper and ceramic this allows manufacturers to build high power structures which are the basis of our power electronics today.

Wafer / Semiconductor
Semiconductors are a core that our electronics are formed around. To shape this core we can use many different tools to design, connect, test and confirm the desired functionality is achieved.
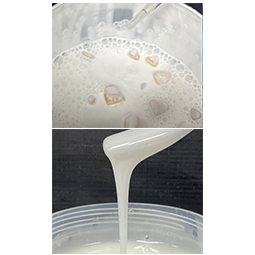
Slurry manufacturing Paste manufacturing
Liquefying materials for the production processes used nearly in every product of our life. Binders and vehicles are mixed with the desired materials and processed to achieve the desired final product shape and parameters such as size, density and thickness.
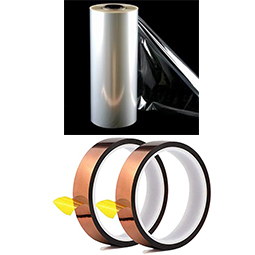
Heat Sensitive Materials Processing
Some materials we like to use in our products are not able to be processed e.g. over 100 C and therefore pose a challenge for processing. UV drying and special inks can still allow customers to implement their designs.
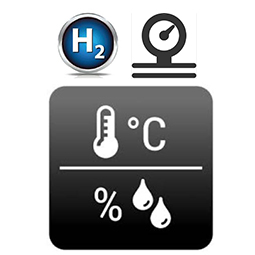
Sensors
Nearly ever product we use today has a sensor to document and react to their environment to create smart devices. Most sensors are exposed to some sort of destructive environment and need to operate in e.g. temperature, acidic, abrasive and harsh environments.

Roll To Roll
One of the biggest challenge of productions is the operator influence. If the processes can be implemented in R2R productions the production efficiency can be increased with less material damages, the throughput can be increased and the overall cost be reduced per circuit.
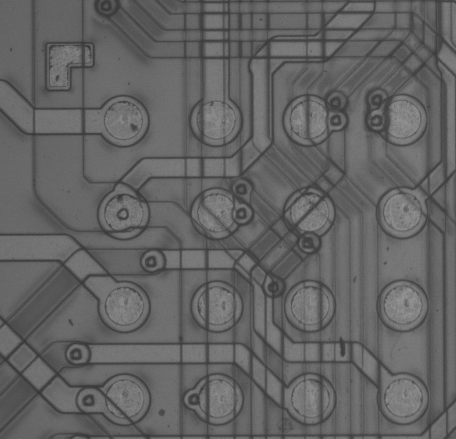
Thin Film
For expensive materials or very specific requirements productions can use thin film processes to create conductive layers. These structures in the meantime also have reached very small sizes but have a lower level of flexibility.
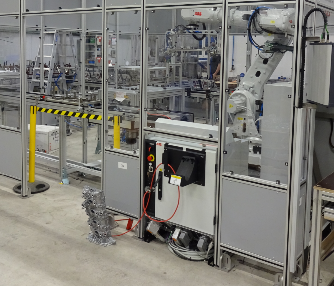
Automation / Assembly
Where economic and necessary processes can be fully automated with present technology. This includes assembly processes, handling, testing and packaging processes.Our partners provide mostly semi-automatic to fully automatic machines even up to smart factories with full live production monitoring.
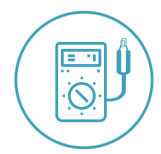
Electrical testing
To confirm functionality electrical measurements are performed on the partial or completed circuits and products. Specialized equipment will allow scrap reduction and product improvements.
